浙江在线-宁波频道3月30日讯(浙江在线 共享联盟宁海站 蒋攀 华建平 罗孙志 记者 陈醉)轿车也流行减肥?!
一项数据道出了轿车不得不减肥的因由:轿车每减重100公斤,百公里油耗降低0.3至0.6升。随着国家燃油指标、环保指标的要求提高,以及电动汽车行程问题的凸显,汽车材料轻量化炙手可热。
那么轿车的减重“轻骑兵”又是谁呢?宁海四十年老牌汽配模具企业——宁海县第一注塑模具有限公司“押宝”在了微孔发泡注塑模具的研发和制造。
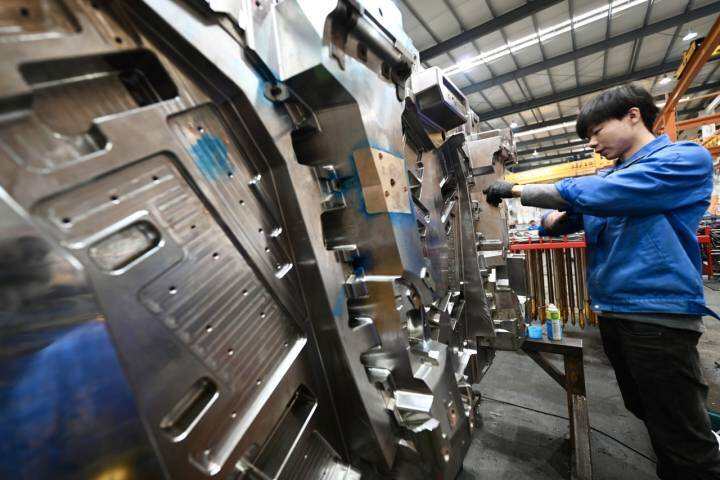
“微孔发泡注塑制品的截面结构如同‘三明治’,两个光滑的外表面中间密布尺寸从十到几十微米的封闭微孔,空气占据了塑料材质的空间,从而减少了本身的塑料含量,达到减轻体重的效果。”第一注塑模具副总经理丁波这样形容道。而要将这种特殊注塑成型汽配部件,应用到汽车减肥上,化学微孔发泡注塑成型工艺就涉及到在塑料注塑过程中放入化学发泡剂,发生化学反应,放出二氧化碳而形成气泡。于是乎,注塑模具就变得至关重要了。
“第一注塑模具”是汽配模具行业里的“老司机”,一直为宝马、奔驰、一汽大众、上海通用、上汽等国内外著名的汽车企业开发大型零部件的模具。从2013年开始研发和制造物理微孔发泡注塑模具,并取得优异的市场占有率。2020年,他们开始着手研发化学微发泡注塑成型的汽配模具,想他抢占汽车轻量化而带来的新市场,并在当年实现1500万的销售收入。
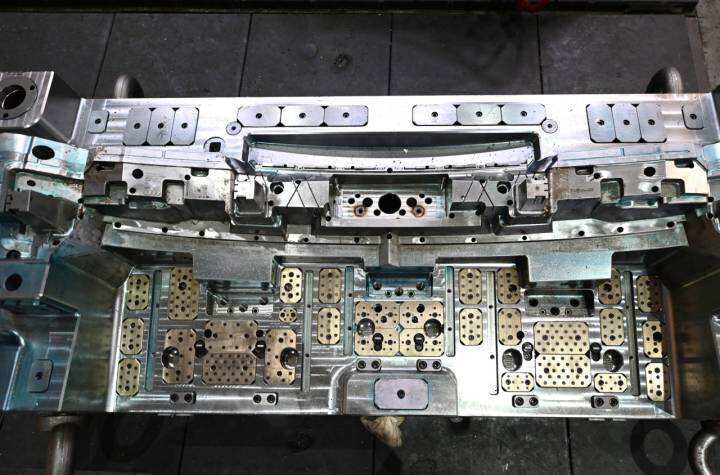
新模具研究困难重重。原来的普通汽配注塑模具对温度、转速、背压都没有特别严苛的要求,同一副模具的各个角落冷却温差达到五六度很正常,但是,塑料的微孔发泡靠的是温度、压力等的精准控制,流程长、温差大,意味着发泡不均匀,产品表面就会出现鼓包、银丝、橘皮纹、色差不一致等等问题。
为此,公司在研发团队人力、加工设备、试模设备上做了很大投入,经过半年时间的摸索和试验,快速掌握了此项技术的关键点。“比如,我们在发泡中容易鼓包的地方,增加排气口,均匀布置冷却系统,使得整个模具的温差控制在2度以内!”丁波说道。
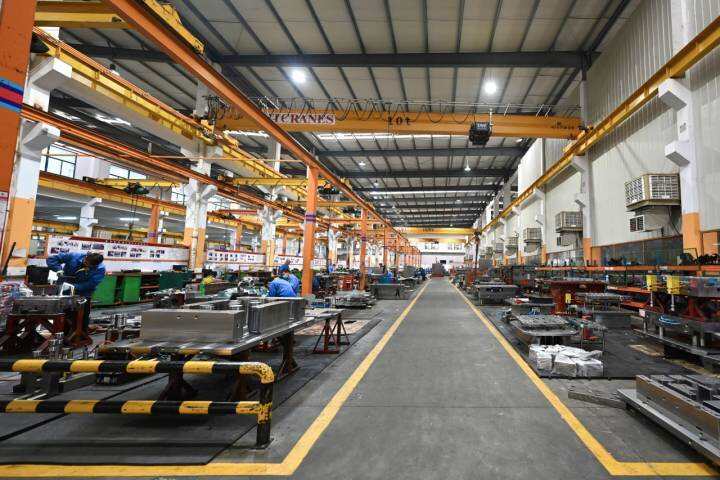
2020年,“第一注塑模具”研发生产的化学微发泡模具正式推上市场,当年,就拿下了八套订单,今年3月份,一家汽车公司直接下了1000万元的大订单。
目前,塑料部件在国内汽车上占重量的10%左右,在国外汽车上达到了15%至20%。“我们的微孔发泡技术能使塑料部件的重量降低15%至30%,可广泛应用于仪表板、门板、柱护板、中央通道、椅背板、通风管道、电机支架等内外饰件,市场非常广。”丁波信心满满地说道。今年,企业预计模具产值能达到2.5亿元。